Amélioration de la fiabilité des installations, réduction des temps d’intervention…
Les clients de Valoris Consulting font face à de nombreuses problématiques. Nos Consultants se concentrent donc sur des domaines tels que la criticité des machines, la maintenance préventive, les stocks, les achats, la gestion des ressources ou les coûts.
Trop souvent, la fonction Méthodes Maintenance n'est pas assez développée voire inexistante. Et pourtant, elle est la condition sine qua non pour passer de l'entretien à la Maintenance.
Aussi, nous pouvons mettre en place et/ou optimiser cette fonction selon vos besoins et vos installations, dans les domaines suivants :
Les clients de Valoris Consulting font face à de nombreuses problématiques. Nos Consultants se concentrent donc sur des domaines tels que la criticité des machines, la maintenance préventive, les stocks, les achats, la gestion des ressources ou les coûts.
Trop souvent, la fonction Méthodes Maintenance n'est pas assez développée voire inexistante. Et pourtant, elle est la condition sine qua non pour passer de l'entretien à la Maintenance.
Aussi, nous pouvons mettre en place et/ou optimiser cette fonction selon vos besoins et vos installations, dans les domaines suivants :
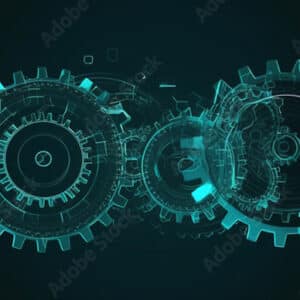